全國服務熱線
0512 - 36605990
18302125233
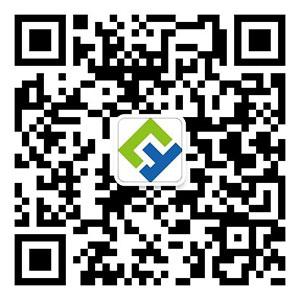
企業(yè)微信
一、光洋產(chǎn)業(yè)株式會社成立于1958年,在日本有九大業(yè)務板塊,我們水性壓敏膠制品是其中之一。光洋產(chǎn)業(yè)目前在中國獨資投資有兩家工廠,一家授權代理銷售公司。其中沈陽工廠主要生產(chǎn)木工用水性膠粘劑,上海工廠生產(chǎn)汽車內飾壓敏膠帶及來料涂膠加工,膠粘劑原料均由日本工廠提供。
二、我介紹一下KOYOBOND水性壓敏膠產(chǎn)品的開發(fā)背景和水性壓敏膠帶物理粘接性能的可靠性。我們開發(fā)水性壓敏膠的第一個原因,是因為我們日本的沼津工廠發(fā)生過一次火災,就是由于溶劑性膠黏劑引起的。溶劑性的膠黏劑本身是易燃易爆的物質,溶劑膠因為含苯類、酯類或醇類等有機溶劑,不易倉儲運輸,易發(fā)生燃爆風險。而且在涂覆生產(chǎn)過程中也會有溶劑的揮發(fā),需要做氣體捕捉收集和防靜電處理,因而生產(chǎn)加工風險也比較高。而且溶劑性的膠黏制品因為殘留有苯類、酯類、醚類溶劑,所以后期也會存在較大刺激性氣味。這次火災就警示了我們開發(fā)水性壓敏膠粘劑的必要性。第二個原因是人們環(huán)保意識的逐漸加強,政府方面日益嚴苛的生態(tài)保護法律法規(guī)都開始陸續(xù)出臺,去年開始我們業(yè)內在上海的大部分溶劑性壓敏膠帶生產(chǎn)企業(yè)都開始往外遷出,有一些規(guī)模比較小的企業(yè)因為承受不了環(huán)保整改的成本,都主動關停或轉行了。在汽車行業(yè),VOC及氣味、ELV等企標、團標逐漸的更新、完善,以及汽車消費者對汽車車艙的氣味與VOC嚴重關切,前面各位專家也已經(jīng)通過各種抽樣調查數(shù)據(jù)佐證了,甚至包括家電行業(yè)目前也在推行無溶劑膠粘制品的行業(yè)標準。這也激發(fā)了我們堅持做水性壓敏膠制品的動力。
接下來我介紹一下我們的KOYOBOND壓敏膠產(chǎn)品。因為壓敏膠在大部分應用里都是作為結構性粘接的產(chǎn)品,部分替代螺絲釘、焊接、鉚釘固定、包括傳統(tǒng)的膠水手工涂覆的用途。因為壓敏膠帶具有儲存、運輸、施工方便,厚度均一度高的優(yōu)點,在各個行業(yè)領域都被大量應用。所以說到粘接,拋開物理性能只談VOC和氣味也是不科學的。我們要保證在開發(fā)一種環(huán)保產(chǎn)品的前提是——它一定要具備穩(wěn)定的粘接特性。
這里我就拿我們之前開發(fā)的溶劑性丙烯酸酯壓敏膠和改良的水性丙烯酸酯壓敏膠做一系列粘接性能的對比試驗。溶劑性的壓敏膠產(chǎn)品,甲苯占比20%,醋酸乙酯占比30-40%;水性壓敏膠產(chǎn)品水份占到45%。對比的實驗主要是通過兩大類試驗,一共是六個小類。四種環(huán)境條件下做180°剝離力測試,以及兩種環(huán)境下的壓敏膠老化試驗。
樣品制作的條件,選用兩種壓敏膠帶,一種是溶劑系KR-159PW,一個是改良水系的KR-162PW。采用兩種PU海棉,分別是聚脂和聚醚,密度都是30kg/m³。把兩種壓敏膠分別和兩種材質的PU海綿貼合在一起,截取10t*15*200mm的樣條,分別貼在SUS304和PP板材上,在常溫常濕條件下養(yǎng)生七天后,分別置于高溫高濕、高溫、溫水、長期高溫四種測試環(huán)境,然后按照300mm/min的速度做180°剝離,對比剝離力。
第一個是將聚脂、聚醚海綿背膠貼合SUS304和PP板高溫高濕條件下做的剝離力對比,在80℃的溫度,95%濕度環(huán)境放置96小時以后,做剝離。通過剝離力數(shù)值看出兩款壓敏膠貼合的聚脂、聚醚海綿在SUS304和PP板上的剝離力基本上是一致的。
第二個是將聚脂、聚醚海綿背膠貼合SUS304和PP板80℃的溫水里面浸泡72小時,然后再放到60℃的烘箱放置8小時,然后取出做180°剝離。我們發(fā)現(xiàn)水性壓敏膠貼和聚脂海綿在SUS304上的剝離力比溶劑性壓敏膠還要高;在低表面能的PP板上僅稍低于溶劑性壓敏膠的剝離力。而水性壓敏膠貼合聚醚海綿的優(yōu)勢就非常明顯,我們水性壓敏膠比溶劑性壓敏膠的剝離力表現(xiàn)更好。
第三個是長期耐高溫的測試,把樣件放到100℃的恒溫下,放1300個小時。因為聚酯背膠海綿在這樣的高溫下不能堅持這么長時間,海綿已經(jīng)碎裂,沒辦法做180°剝離力。而聚醚海綿背膠還可以做180°剝離力,從表中可以看出貼合溶劑性壓敏膠的聚醚海綿在SUS304上的剝離力是7.0N/15mm,貼合水性壓敏膠的聚醚海綿剝離力是7.9N/15mm;在PP板上也是貼合水性壓敏膠的聚醚海綿要比貼合溶劑性壓敏膠的聚醚海綿180°剝離力要高;做剝離的時候都是把海綿給剝壞了,膠膜沒有從SUS304和PP板上脫離。
第四個長期高溫高濕測試,把樣件在80℃、95%濕度環(huán)境下放置1200小時后做180°剝離。貼合聚脂海綿,水性壓敏膠和溶劑性壓敏膠在SUS304和PP板上的剝離力相當,而貼合聚醚海綿,水性壓敏膠卻好于溶劑性壓敏膠的剝離力。
第五個和第六個試驗分別是耐熱老化及耐水老化。兩種海綿背膠材質不變,貼合的材質依然是90°折彎的SUS304和PP板,不過在折角的地方將10t*15w*200mm的海綿做90°角貼合,其中一個端頭貼合尺寸是10t*15w*10mm,再用1KG橡膠壓輪按照300mm/min的速度往復加壓兩次,常溫常濕養(yǎng)生7天。
耐熱老化是將養(yǎng)生后的樣件在80℃恒溫烘箱放置10天,看短頭的海綿會不會脫膠彈起來。
耐水老化是將養(yǎng)生后的樣件在80℃水中浸泡10天,然后60℃烘箱里放置8小時,看短的海綿端頭是否會脫膠彈起來。通過實驗證明,無論是溶劑性壓敏膠還是水性壓敏膠,短端頭海綿都沒有脫膠彈開。
通過上面一系列實驗,可以得出這么一個結論,就是我們改良的水性壓敏膠和溶劑性壓敏膠是具有同樣的耐熱、耐水耐老化性能的。我們?yōu)槭裁茨茏龅剑烤褪且驗槿毡竟庋筇赜械姆磻腿榛瘎┘敖宦?lián)劑的應用。我們日本研究所前后花了近八年時間,才找到最匹配丙烯酸酯的反應型乳化劑和交聯(lián)劑,同時在探索最佳的添加比例和添加時機上也付出了很多心血。
三、接下來就開始談我們產(chǎn)品在環(huán)保性能上的特點及驗證。
剛才一汽的朱熠主任,提到了丙烯酸酯膠粘制品的氣味較大的問題,我們這個壓敏膠產(chǎn)品雖然也是丙烯酸酯聚合物,但是呢,丙烯酸酯的膠粘劑也分很多種,有溶劑性,有水性,也有UV固化型。不同形態(tài)的丙烯酸酯膠粘劑,氣味和VOC表現(xiàn)也是截然不同的。
VOC根據(jù)對應沸點可以分為VVOC,VOC和SVOC。目前行業(yè)里 參照比較多的VOC測試方法就是德國汽車工業(yè)協(xié)會的VDA標準和日本的袋子法。
而氣味和VOC是否有關聯(lián)呢?前面有專家在做報告的時候也講過這個問題了,其實氣味和VOC實際上有太大的關聯(lián)性。降低氣味不一定有效降低VOC,降低VOC也不確保一定能降低氣味。我們每個人嗅覺閾值都有差異,因此部分主機廠有時候會沿用國外的材料,但是沿用過來以后,發(fā)現(xiàn)做氣味測試的時候,并不確保氣味完全達標。我認為在不同環(huán)境的、不同飲食習慣、不同化學品使用背景的人,嗅覺閾值差異很大。我們大多人對不熟悉的味道往往是比較排斥的,這就是說外國人覺得氣味低或不難聞的氣味,中國人就可能覺得氣味大,甚至無法忍受。但是有氣味就代表有毒嗎?并不是這么回事,跟濃度值的高低有關系;低氣味或無氣味就等于無毒嗎?也并非如此,比如一氧化碳它沒有味道,但是低濃度下它也有強烈的毒性。
我們做水性壓敏膠的目的也是給汽車車艙的氣味和VOC做一個減法,不確保把溶劑性壓敏膠都改成水性壓敏膠,整個車就沒有氣味和VOC了,但是我們努力在做一個減量的工作,給汽車消費者提供更加安全、健康、舒適的乘坐環(huán)境。
下面舉例說明水性壓敏膠和溶劑性壓敏膠的VOC釋放對比,來說明使用水性產(chǎn)品的必要性。根據(jù)測算平均每臺車需要用到壓敏膠不低于5㎡,包含了結構性粘接的壓敏雙面膠及線束用布基膠帶、PVC膠帶、不干膠標簽等。按照100g/㎡的干膠涂膠量計算,每臺車合計用壓敏膠干膠500g。根據(jù)我們掌握的第三方檢測報告,溶劑性壓敏膠的VOC釋放量不小于500μgC/g,再乘以500g就是TVOC=250000μgC。而我們的水性壓敏膠目前VOC釋放的平均水平是小于50μgC/g,再乘以500g就是TVOC=25000μgC,和溶劑性壓敏膠產(chǎn)品的TVOC釋放量相差近10倍。當然考慮到實際裝配應用的情況,無論溶劑性壓敏膠還是水性壓敏膠VOC釋放總量要小得多,但是水性壓敏膠依然具有壓倒性的環(huán)保優(yōu)勢。
汽車的VOC和氣味管控要從源頭開始說了很多年,但大多數(shù)主機廠只對初始的總成件抽查,總成件測試合格了,一般不會再對下面的零部件或材料驗證。除非初始的總成件這邊有VOC和氣味的問題了,才會逐級分解下去找原因整改。但是往往就有材料企業(yè)為了通過材料篩選或拿到合格的三方檢測報告,在試樣階段各種辦法預處理材料,而量產(chǎn)的時候,預處理的方法成本太高就被棄用了,這就是為什么經(jīng)常在試制樣車和批量生產(chǎn)汽車時,氣味和VOC一致性上往往容易出紕漏的原因。因此主機廠建立自己的材料庫以及在加強產(chǎn)線抽查、監(jiān)測,刻不容緩。
我曾經(jīng)在走訪部分做膠帶模切還有海綿貼合加工的企業(yè)發(fā)現(xiàn),工人有時候會把不同用途、不同環(huán)保性能的材料在同一個封閉車間加工、在同一個倉庫存儲,沒有做隔離,這就可能存在交叉污染的問題。這也是我們單獨去送檢我們產(chǎn)品做VOC和氣味是合格的,但是加工企業(yè)送檢的時候就不合格的原因之一。
我分享下我們光洋這邊氣味和VOC的管控經(jīng)驗。首先我們公司對供應環(huán)節(jié),比如膠粘劑里面添加的一些填料、助劑都要進行VOC和氣味的管控,后期制程中包括離型材、包裝材都需要管控ELV和VOC,只有每一個供應環(huán)節(jié)及制程都管控起來才能標本兼治。其次因為我們的壓敏膠是水性的,本身就不含有機溶劑,所以VOC釋放量“天然低”。再則在包裝運輸過程中,采用鐵桶內嵌PP塑料袋裝載膠粘劑,再抽真空,這樣應對環(huán)境溫度的適應性就更強了,最重要的原因就是避免發(fā)酵產(chǎn)生有氣味的物質——丁醇。還有我們改良涂布設備的進出風循環(huán)系統(tǒng),進風口將進氣凈化處理以后導入我們的涂布設備的烘道中。出風口流出的水蒸汽混合物也是經(jīng)過活性炭吸附處理之后再通過煙囪排到戶外,這樣也有效避免了廢氣、異味、噪聲的產(chǎn)生。最后我們的水性壓敏膠半成品采用了低溫熟化工藝,也是為了避免發(fā)酵生成醇類化合物導致異味生成。
下面是我們KOYOBOND水性壓敏膠產(chǎn)品做的部分三方檢測報告。可以看到KR-E308、KR-036/S、KR-162I/S的量產(chǎn)品均有非常好的低VOC低氣味表現(xiàn)。E308N直接涂膠產(chǎn)品做大眾汽車的PV3900最佳成績是C1-C3全部是2.0。而036S和162S也是我們后期重點推廣的低VOC低氣味壓敏膠帶產(chǎn)品,送測VDA270、275、277都是完全達標的。
四、報告的第四部分,是所有主機廠、零部件廠都關心的一個問題了,就是我們KOYOBOND產(chǎn)品的成本。最近《我不是藥神》的電影很火 ,圍繞一個治療線粒性白細胞的藥品展開的。在電影的評論里,有一個意味深長的評論是這樣說的:為什么制造成本僅僅0.5美分的一片藥可以賣到50美元呢?那是因為您買的是第二片藥!但是除了藥廠自身誰會關注第一片藥的成本是5000萬美元+130年呢?!其實任何新技術新產(chǎn)品都存在這樣的邏輯。當我們現(xiàn)有的技術和產(chǎn)品不能滿足客戶需求時,就需要研發(fā)創(chuàng)新,而任何一個從無到有的新產(chǎn)品的開發(fā),必然需要時間、精力、金錢的投入。剛剛我跟一汽大眾的李彥軍主任聊天時說,現(xiàn)在我們開發(fā)一個新的產(chǎn)品出來,都會面臨一個死循環(huán),很多客戶非常認可我們的產(chǎn)品品質,但是因為我們前期生產(chǎn)成本偏高,導致客戶大量更換環(huán)保材料的動力不那么足。但是對于我們來說,我們這個產(chǎn)品只有被客戶大量使用,才會逐步降低生產(chǎn)成本變得更加便宜。如果一開始大家都因為成本高少用或者不用,那我們的生產(chǎn)成本一直居高不下。舉個例子,房租是不變的,電費是白天貴晚上便宜,一條生產(chǎn)線開8小時和24小時的產(chǎn)能相差三倍,但是房租在單位面積的產(chǎn)品分攤上節(jié)省了三分之二,同時能源成本也剩下來了,還不計算因為產(chǎn)能增加帶來的原材料采購成本的降低。如果達標的產(chǎn)品被嫌貴,便宜的產(chǎn)品又被擔心不達標,這就是一個供求雙輸?shù)木置妫彩遣焕谄髽I(yè)創(chuàng)新與研發(fā)新技術、新產(chǎn)品的。
目前市面上常見的壓敏膠產(chǎn)品一共有四類型。一種是完全不符合低氣味低VOC但是黏性很好的溶劑性產(chǎn)品,成本最低;然后是普通的水性無溶劑產(chǎn)品,部分符合低VOC低氣味,但是黏性差一些,成本居中。再有是脫甲苯溶劑性產(chǎn)品,替換苯類溶劑為醇類,醚類、酯類,相對比較環(huán)保,但解決氣味的成本較高。最后是改良型的水性和無溶劑性產(chǎn)品,完全符合低VOC低氣味,黏性也好,但是成本也最高。目前我們KOYOBOND能提供的壓敏雙面膠帶主要有無紡布基材、無基材、PE網(wǎng)格基材、PU泡棉基材這幾種雙面膠帶。針對部分客戶,我們也可以采用來料直接涂膠的方式,相對性價比是最高的。但有一個問題就是,因為很多涂膠的材料都是發(fā)泡材或這無紡布、氈類,按照體積算長途運輸成本高,所以來料涂膠有供貨距離的限制,適合半徑150KM范圍的二級供應商,這個半徑以外的客戶如果自己有涂膠機,我們可以提供壓敏膠水產(chǎn)品和作業(yè)指導。
決定水性壓敏膠帶的成本的主要要素,膠黏劑成本占到產(chǎn)品的25-35%。構成材料像里面的綿紙、離型材等占到整個產(chǎn)品15-25%,生產(chǎn)成本20-30%,管理成本8-12%,其他就是營銷成本6-9%。算下來壓敏膠帶利潤并不高,目前做到15%以上的利潤就很難了。整體上我們的產(chǎn)品單價比市面上常見的日系、歐美系一線品牌的同用途、同類型產(chǎn)品要便宜三分一左右,得益于我們實現(xiàn)了本土化定制生產(chǎn)。
我們盡可能豐富膠粘劑產(chǎn)品的類別,實現(xiàn)產(chǎn)品厚度、寬度、長度、粘性的定制化生產(chǎn),目的就是助力整個汽車內飾行業(yè)兩降一增,降VOC,降成本,增加粘結品質。我們KOYOBOND水性壓敏膠還有一個特點就是抗增塑劑效果特別好。因為增塑劑大多是溶劑性的,如果用溶劑性壓敏膠,增塑劑會溶解到膠膜里面去,時間一長就會導致黃變、脫膠。而溶劑性增塑劑不溶于水,因此水性膠膜反倒不用擔心增塑劑溢出脫膠的問題。
最后說說我們KOYOBOND水性壓敏膠產(chǎn)品的應用,空調出風口海綿粘接、線束降噪海綿粘接、風擋密封條粘接、座椅加熱墊片粘接、方向盤皮革包覆粘接等。目前我們的產(chǎn)品間接供應的主機廠包括一汽大眾、一汽大眾奧迪、上汽大眾、泛亞汽車、北汽奔馳、長安福特、長安馬自達、江淮汽車、廣汽傳祺、日產(chǎn)汽車。所有這些壓敏膠帶的應用,消費者雖然摸不到看不見,但是卻很非常重要!希望各位主機廠、零部件廠和材料企業(yè)的專家能夠給于更多關注,共創(chuàng)車艙綠色生態(tài)!
今后我們還會致力于開發(fā)水性無鹵阻燃壓敏膠,F(xiàn)DA級水性壓敏膠,只有無損于人類健康與生存環(huán)境的產(chǎn)品,才是真正的好產(chǎn)品!我的報告結束了,再次謝謝大家的聆聽!